What are the Challenges of Lighting Aircraft Hangars?
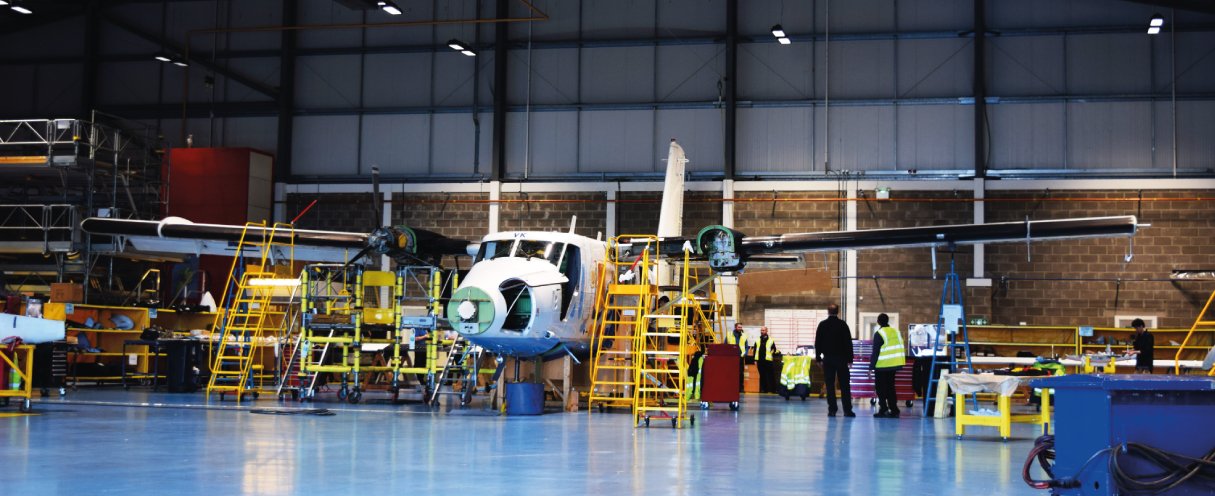
Lighting aircraft hangars poses several unique challenges due to the specific requirements of such large, multifunctional spaces. These challenges stem from the need for high lux levels, uniform illumination, safety considerations, maintenance needs, and energy efficiency. Here’s a breakdown of the main challenges and their design implications:
1. High Ceilings and Large Open Spaces
- Challenge: Hangars are typically vast, open spaces with high ceilings (often 15m or more). Airline and 3rd-party maintenance operators require flexibility; whether for military, national carriers, or private use, an individual hangar can be used to maintain a variety of aircraft sizes. Subsequently, lighting needs to reach most areas where maintenance work occurs, including both high up (at tail or rotor height) and down at ground level (at landing gear height).
- Implication: Standard light fixtures may not be able to produce enough light and distribute it appropriately to illuminate all required areas effectively. Lighting simulations must include calculation surfaces at a variety of maintenance heights to demonstrate suitability. Specialised high-output high-bay fixtures with carefully selected optics, or supplemental lighting at lower levels is often needed, which can be costly and sometimes more complex to install.
2. Uniform Illumination and High Lux Levels
- Challenge: Aircraft maintenance requires high visibility and attention to detail, meaning that required light levels can be very high (>1500lux), but shadows, and dark spots must be minimised. Irregular lighting can result in poor visibility and create safety hazards.
- Implication: Desired lux levels should be established subject to the hangar's use. Achieving uniform light distribution (mitigating shadows or high spots) often requires careful light fixture placement and optic selection. Narrow beam angles assist is achieving higher lux levels at the ground (and lower glare), however narrow optics typically decrease uniformity at higher level. Increasing the number lights while reduing their light output, typcially imroves uniformity, but normally increases overall cost. Lighting designers need to run multiple configurations to identity the optimised solution.
3. Colour Accuracy
- Challenge: Detailed maintenance and inspection work demands excellent color rendering to accurately identify issues like cracks, corrosion, or wiring discrepancies.
- Implication: Alongside a high total lumen output, the hangar lighting needs to have a high Color Rendering Index (CRI); ideally above 80. Luminaire efficacy typically reduces with higher colour rendering so it comes at an up-front and operational cost. LEDs are preferred as they can offer high CRI with lower energy use than traditional lighting.
4. Temperature and Environmental Resilience
- Challenge: Hangars often experience extreme temperatures due to their large, open structures. In hot climates, e.g. in the Middle East, temperatures can soar (even in the shade), while in cold environments, lighting fixtures might face sub-freezing conditions. Temperature can affect lighting performance. High temperatures are particulalry concerning because they can lead to accellerated lumen degradation of the light source (typcially LED) and the LED drivers.
- Implication: Where extreme conditions occur, durable lighting solutions must be chosen. LED lights, for example, perform well in cold temperatures but fixtures with high temperature tolerance may be required for hangars in hot regions. Features may include, LED chips with high lumen maintenance (e.g. L90B10> 50,000hrs), drivers with published lifetimes >100,000hrs, and specially designed heat-sinks.
5. Glare Reduction
- Challenge: Due to high lumen requirements, glare can easily become an issue. This can be direct, or indirect via reflective surfaces on aircraft and hangar floors.
- Implication: Positioning lights with narrow optics at specific angles and/or adding diffusive covers can help manage direct glare. Lighting simulations should report direct glare calculations across appropriate observation angles and positions in 3D space. These simulations need to incorporate the photometric data of fixtures, including all proposed optical accessories. Indirect glare from reflective hangar floors is more challenging to evaluate in simulations (common with designing swimming pools and indirect glare off the water surface). In this instance, narrow beam angles can be counter-productive, so care and an element of best judgement may be required. Using more fixtures at lower lumen outputs can help minimise both direct and indirect glare, though it often raises product and installation costs.
6. Energy Efficiency and Cost Management
- Challenge: Hangars often operate nearly 24/7, leading to high energy demands. Moreover, high ceilings and the expansive areas, and restricted scheduling, make maintenance costly and disruptive, so long-lasting, energy-efficient lights are essential.
- Implication: LED lighting is typically chosen for its lower energy consumption and longer lifespan, which reduces both operating costs and maintenance frequency. Many hangars are also incorporating motion sensors, dimmers, and smart lighting systems to reduce usage when the area is unoccupied, or in use for different applications.
7. Emergency and Backup Lighting
- Challenge: Aircraft hangars must be equipped with emergency lighting systems to ensure safe exit paths in case of power failures. Back-up lighting may also be required to maximise continuity.
- Implication: Emergency lighting systems are essential for safety and compliance. They require dedicated "non-maintained" fixtures or dual-function "maintained" lights, adding to the complexity and initial setup costs. Self-test or DALI self-test fuctionality can reduce regular inspection and provide remote reporting features via hard-wired or wireless control systems. Site generators running the general lights are typically the most cost-effective method for backup lighting.
8. Lighting Controls and Zoning
- Challenge: Hangars often need variable lighting for different sections and tasks, such as aircraft inspection, maintenance, and general workspaces.
- Implication: A lighting control system that can zone and adjust lighting levels for specific areas can be extremely cost-effective, allowing energy conservation and meeting the varying lighting needs of different activities. Zoning can be hard-wired or wireless. Control can be manual, via physical or virtual switches, or by the use of motion sensors to dim or switch off lighting in unused sections of the hangar.
9. Compliance with Regulatory Standards
- Challenge: Aviation and occupational safety standards impose specific requirements for lighting in aircraft maintenance facilities, including minimum lux levels and color rendering properties.
- Implication: Hangar lighting must comply with standards such as those set by national administrations, e.g., the Civil Aviation Administration (CAA) in the UK, or the Federal Aviation Authority (FAA) in the USA. Failure to do so may require expensive adjustments to meet standards.
10. Maintenance Accessibility
- Challenge: High ceilings make it challenging and costly to reach fixtures for maintenance and repairs, requiring lifts or scaffolding that can disrupt hangar operations.
- Implication: Long-lasting and low-maintenance lighting solutions, such as LEDs with lifespans of L90B10> 50,000hrs hours or more, reduce the frequency of fixture replacements and repairs. An increasing number of facilities are adopting remotely accessible lighting controls to reduce the need for physical adjustments, and reporting of component status via the DALI2 standard.
Conclusion
Given these challenges, lighting solutions in aircraft hangars need to be carefully planned, with a strong emphasis on energy-efficient, low-maintenance, and durable fixtures that meet stringent safety and visibility requirements. Implementing smart lighting systems, using LED technology, and incorporating specialised anti-glare and high-CRI features are crucial to addressing these challenges effectively.