How Important is Corrosion Resistance in LED Lighting?
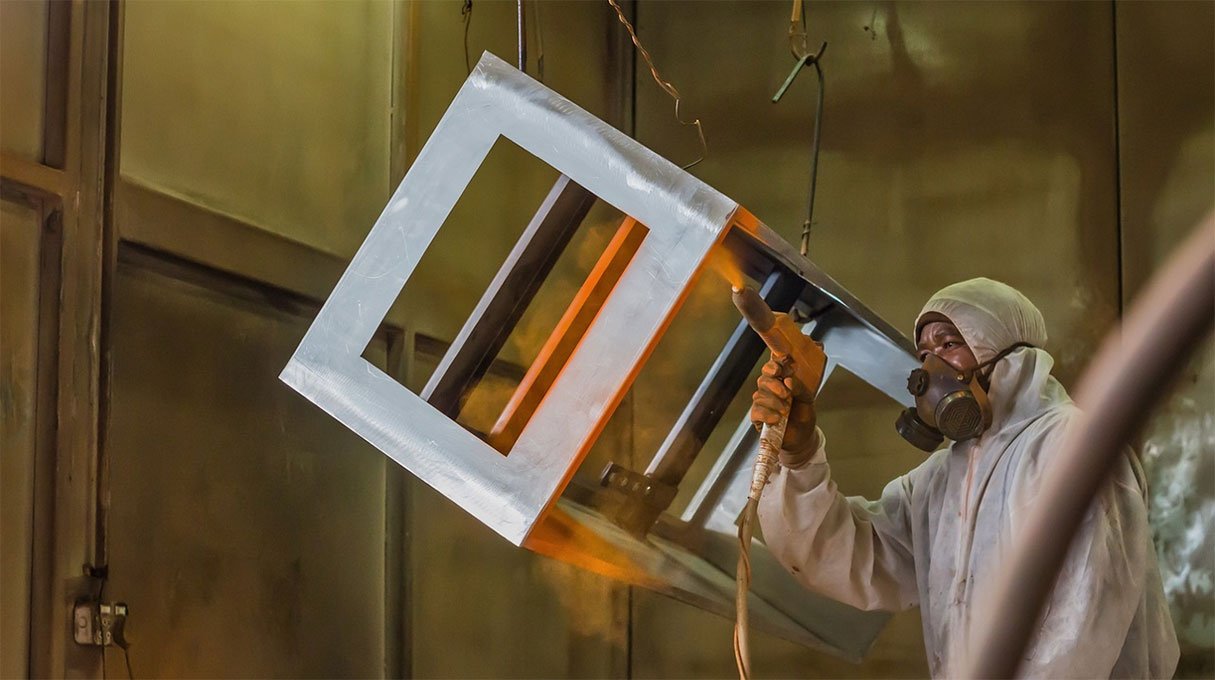
For many industries like offshore oil and gas, where harsh environments are prevalent, the longevity of light fixtures is greatly impacted by corrosive atmospheres. As Health and Safety are often critical in these working environments, adequate levels of illumination must be maintained to provide a safe environment for employees. Therefore, frequent and sustained failures in lighting installations can be incredibly costly for companies in these sectors.
Key Takeaways
- Corrosive environments, such as those found in offshore oil and gas industries, can significantly reduce the lifespan of standard LED lighting fixtures.
- Implementing corrosion-resistant LED lighting enhances safety by ensuring consistent illumination in critical areas.
- Investing in corrosion-resistant fixtures leads to long-term cost savings by minimising maintenance and replacement expenses.
- Selecting appropriate materials and protective coatings is essential for maximising the durability of LED lighting in harsh conditions.
However, the longevity of light fittings operating in harsh environments can be prolonged by ensuring that the lights are corrosion-resistant to the necessary degree.
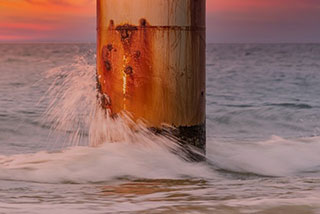
What Causes Corrosion?
Corrosion is a chemical reaction where a Gas or Liquid causes a solid material to degrade aesthetically and structurally over time. The corrosion process is often accelerated by catalysts such as high temperatures, acids, and salts. Surface Characteristics like Rust, Patina, Discolouration, and Flaking Paint typically indicate that corrosion has occurred on a surface. For light fittings, corrosion is normally experienced when humidity, chemicals, and pollutants are present.
The Impact of Corrosion on Light Fittings
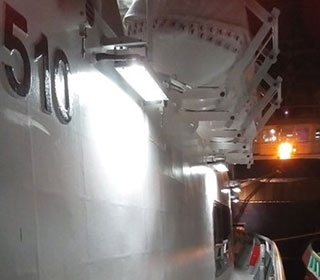
Corrosion can impact light fittings both structurally and electrically. Over sustained periods, corrosion can lead to loss of material, which can lead to hardware breakages, and potential safety risks from falling debris. When corrosive gas/liquid penetrates electrical connections, conductivity will be adversely affected, and eventually, the light will fail.
However, these are extreme scenarios – Corrosion resistance will most typically first attack the exposed cosmetics of the lighting product, which may impact protective properties such as ingress protection or thermal management. As such, corrosion, even in less severe cases will eventually cause failure through indirect effects such as water ingress or overheating.
Protecting Lights against Corrosion
Preventative measures can be taken to reduce corrosion experienced in light fittings.
Paints and Coatings
Using protective paints and coatings as a barrier method restricts the degree of surface exposure to corrosive elements. The most commonly used method is Powder Coating, where exposed surfaces are covered and sealed within a plastic/polymer powder. For corrosive environments, like marine applications, it is recommended that Powder Coatings should have a minimum thickness of 80 microns to increase longevity.
Electrolytic Passivation (Anodising)
Anodising is an additive process used to increase the thickness a materials Oxide layer, which increases resistance to surface defects. However, imperfections in the anodising process can still lead to corrosion. As such, Aluminium Alloys are most commonly anodised to improve durability, and subsequently sealed to improve corrosion resistance.
Material Properties
Certain types of materials are more resistant to corrosion, therefore, selecting the appropriate material for the intended use and environmental factors is paramount.
Aluminium
Particular Aluminium Alloys containing increased levels of Magnesium and Silicon have improved corrosion resistance:
Aluminium Grades 6061 and 6063 have good resistance against standard corrosive agents.
Aluminium Grade 5083 has the highest levels of Magnesium and Silicon in its composition and is known as the "Marine-Grade Aluminium" as it offers excellent protection against saline solutions (saltwater).
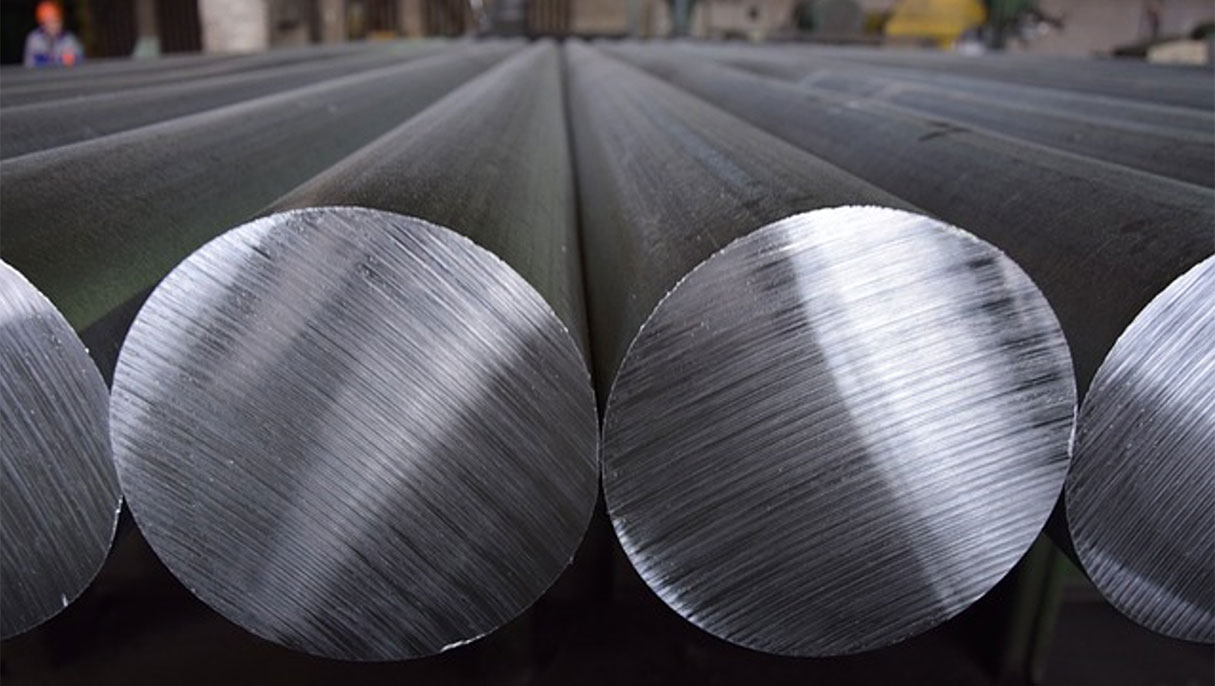
Galvanised Steel
A Zinc Coating, applied to Steel during the galvanising process, forms a protective barrier between corrosive agents and the base metal protecting against defects, discolouration, and corrosion.
Stainless Steel
Stainless Steel is an Iron Alloy which contains a small amount of Chromium. The Chromium forms a passive film which reacts with oxygen to self-heal and protect the material. Due to these properties, Stainless Steel is deemed the most appropriate material for corrosive environments.
Adding increased levels of Nickel to the Alloy further improves the corrosion resistance of the material. Grade 304 is used more commonly for non-severe environments. However, chloride environments require increased protection, and Grade 316 Stainless Steel is most appropriate.
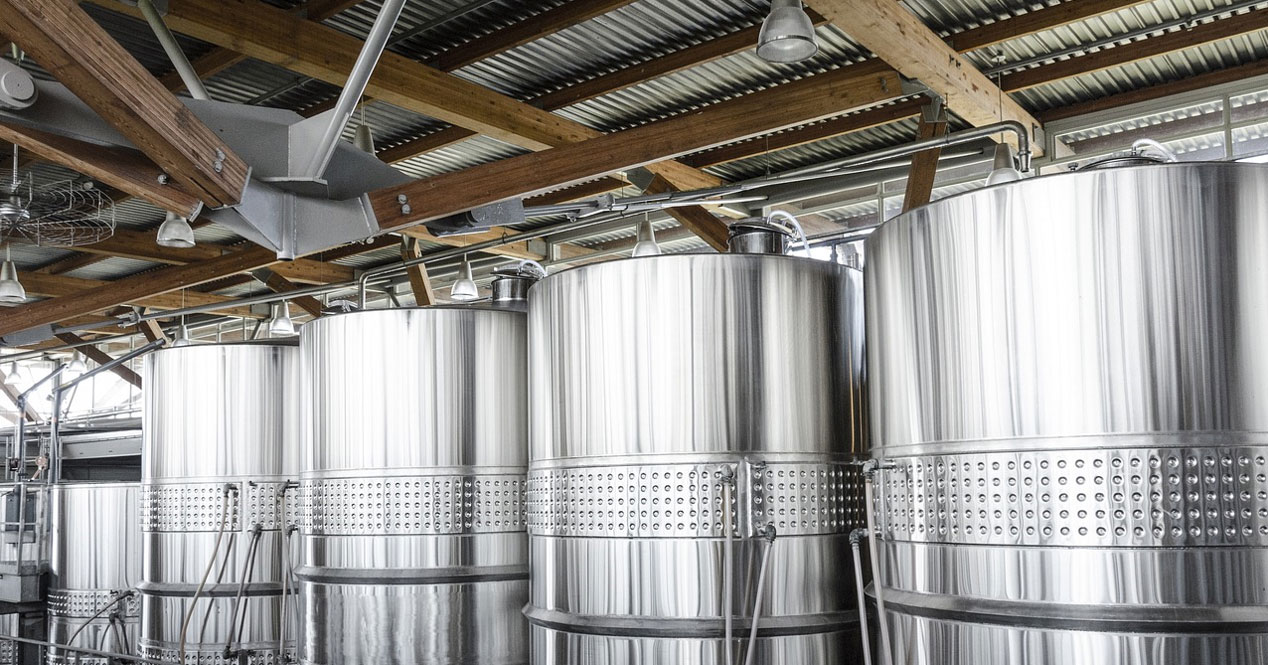
Environmental Corrosion Classification and Testing for Outdoor Environments
The ISO12944 Standard informs industry professionals of application-specific corrosion resistance requirements. There are 6 classifications (C1 to CX) for outdoor "increasingly-salt-water-based" corrosive environments based on long-term surface degradation and material loss. These classifications can be used to ensure suitably protected lights are installed in inland to off-shore atmospheres. These are outlined in the table below:
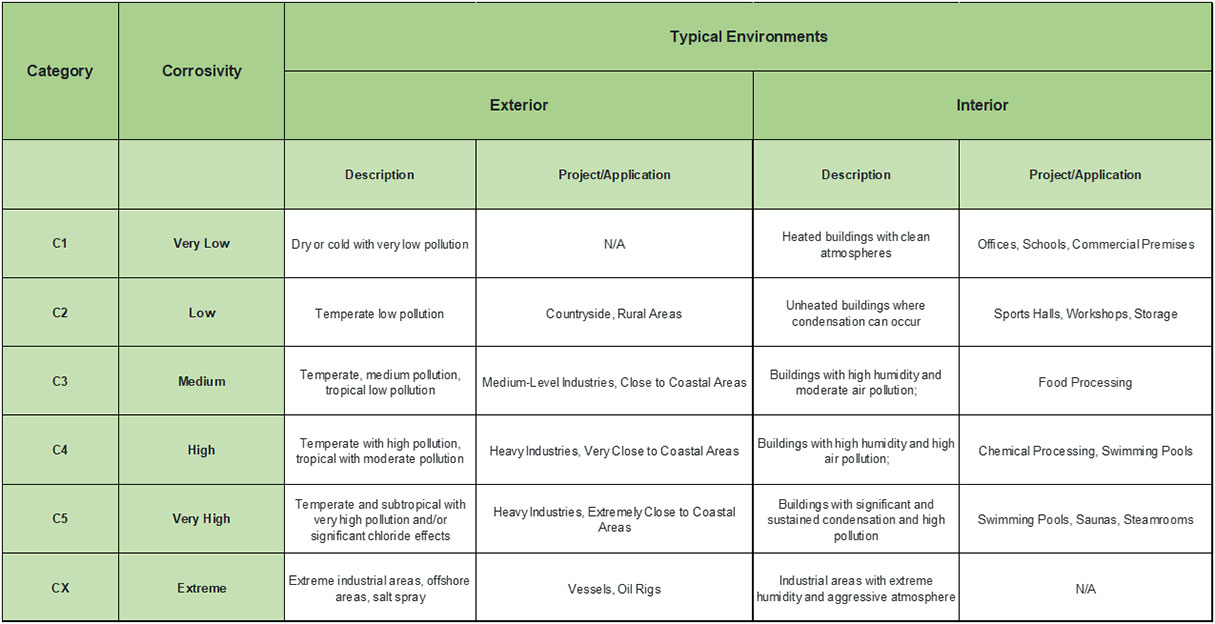
To ensure that light fittings meet the requirements of their respective environments, manufacturers implement exposure tests which examine the performance of lighting products within simulated environments. Tests are typically implemented for a set duration, and the performance results are then extrapolated to predict realistic product longevities within these environments. Most commonly, manufacturers use Salt Spray (ASTM B117), Cyclic Corrosion (ISO16701), and Humidity (ASTM D4585) tests to assess corrosion resistance.
Finding Suitable Corrosion Proof Lighting
Ensuring the most appropriate lighting for your environment is purchased ensures product longevity, reduces maintenance costs, and improves lighting performance.
Before purchasing lights for, consideration should be given to:
Installation Environment
- Dry Indoor Environments typically require C1 Classified Lighting.
- Outdoor Environments typically require at least C2 Classified Lighting.
Location
- Low Pollution Areas (Rural) are exposed to less corrosive agents and can typically use C2 Classified Lighting.
- Urban and Industrial areas are more exposed to airborne contaminants and require C3 Classified Lighting.
- Coastal Areas have increased exposure to Saline and require C4 Classified Lighting as a minimum.
Additional Characteristics
- Areas with increased or sustained humidity/condensation/moisture may require higher protection against corrosion. In these instances, C5 or CX Classified Lighting will be most appropriate.
Lighting Components and Fixings
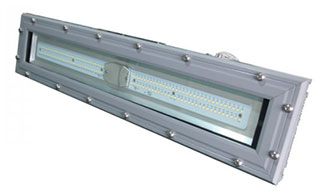
- The materials used within the light fitting should be appropriate for the environment. High-Grade Stainless Steel and Aluminium offer the best protection against corrosion.
- Paints and Coatings provide an additional barrier between corrosive agents and base materials. Marine-Grade Powder Coating offers the highest degree of protection against corrosion.
Conclusion
In environments where corrosive elements are present, the importance of corrosion-resistant LED lighting cannot be overstated. By choosing fixtures designed to withstand harsh conditions, industries can ensure safety, reduce maintenance costs, and achieve reliable, long-lasting illumination. Prioritising corrosion resistance in lighting solutions is a prudent investment that pays dividends in both performance and durability.